Constant improvement: Delivering commercial progress through research and development
BY GEOFF SMITH
CHIEF TECHNOLOGY OFFICER
Geoff leads the engineering function, focusing on technology design and development. He has seven years’ experience in pyrolysis plant development and operation
A well-worn saying is that nothing worth having comes easily. This is true for any ambitious goal, and especially when that goal is to see a shift across an entire industry, and global system of working. At Itero, we apply this wisdom to our work in chemical recycling and our goal of supporting the broader transition to a circular economy for plastics. Realistically, we’re all still in the early days of changing our relationship to plastic and recycling. Making the shift will take effort, knowledge, and cooperation. This is where research and development come in.
Research and development (R&D) is crucial to our long-term success, because if nothing good comes easily, it also doesn’t come immediately. In 2020, Itero completed commissioning our R&D plant in Iver, Buckinghamshire. Despite several challenges along the way, we have made great progress and I am very proud of our team for driving us this far. Our on-site engineers have been especially brilliant throughout, having had to juggle the roles of maintenance engineer, operator, researcher and innovator.
Our R&D plant is a small-scale version representing our 27 kilotonne per annum at-scale plant at the Brightlands Chemelot Campus in Geleen, Netherlands, and we’ve just raised €6m in investments for the next stages of our Netherlands-based project. As R&D at our Iver plant is crucial for the delivery of our Netherlands plant, R&D will receive a proportion of this investment.
With our Iver plant we have been able to test in real-world conditions how different waste plastic feedstocks react in our pyrolysis process, validating and iterating our hypotheses and skills. Importantly, we are building up an understanding of the impact of contaminants and impurities on both our operation and offtake product quality. While furthering our understanding of the chemistry, we’re also economically driven to optimise the process to maximise our product yield and quality. Everything we do is assessed as part of our comprehensive R&D schedule, which is running alongside the development of our Brightlands plant.
Our R&D schedule has been organised around the three key focuses of the advanced recycling process; offtake (product), plant process, and feedstock (input). To ensure commercial success at our future plants, understanding the characteristics of the recycled pyrolysis oils takes centre stage.
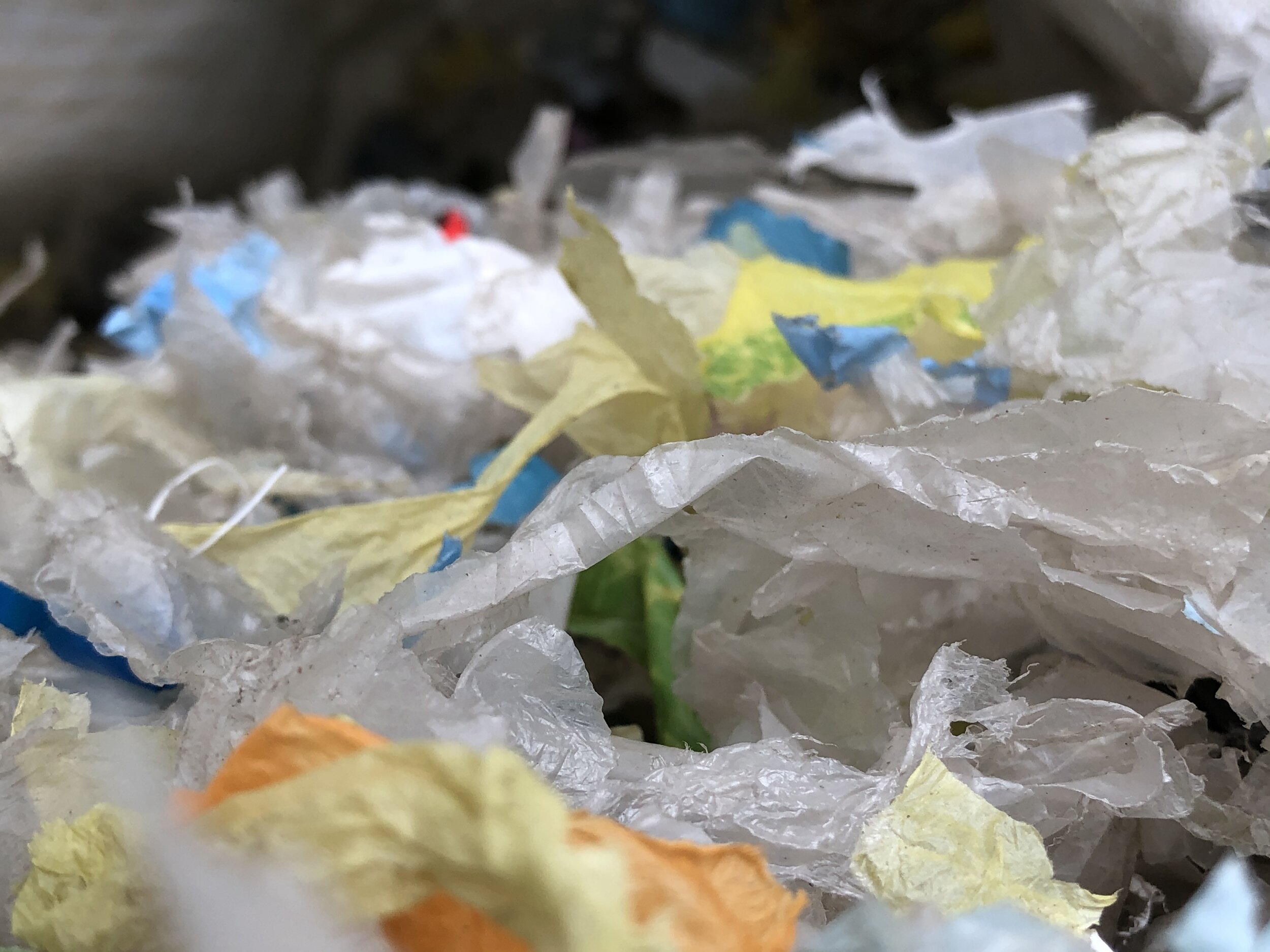
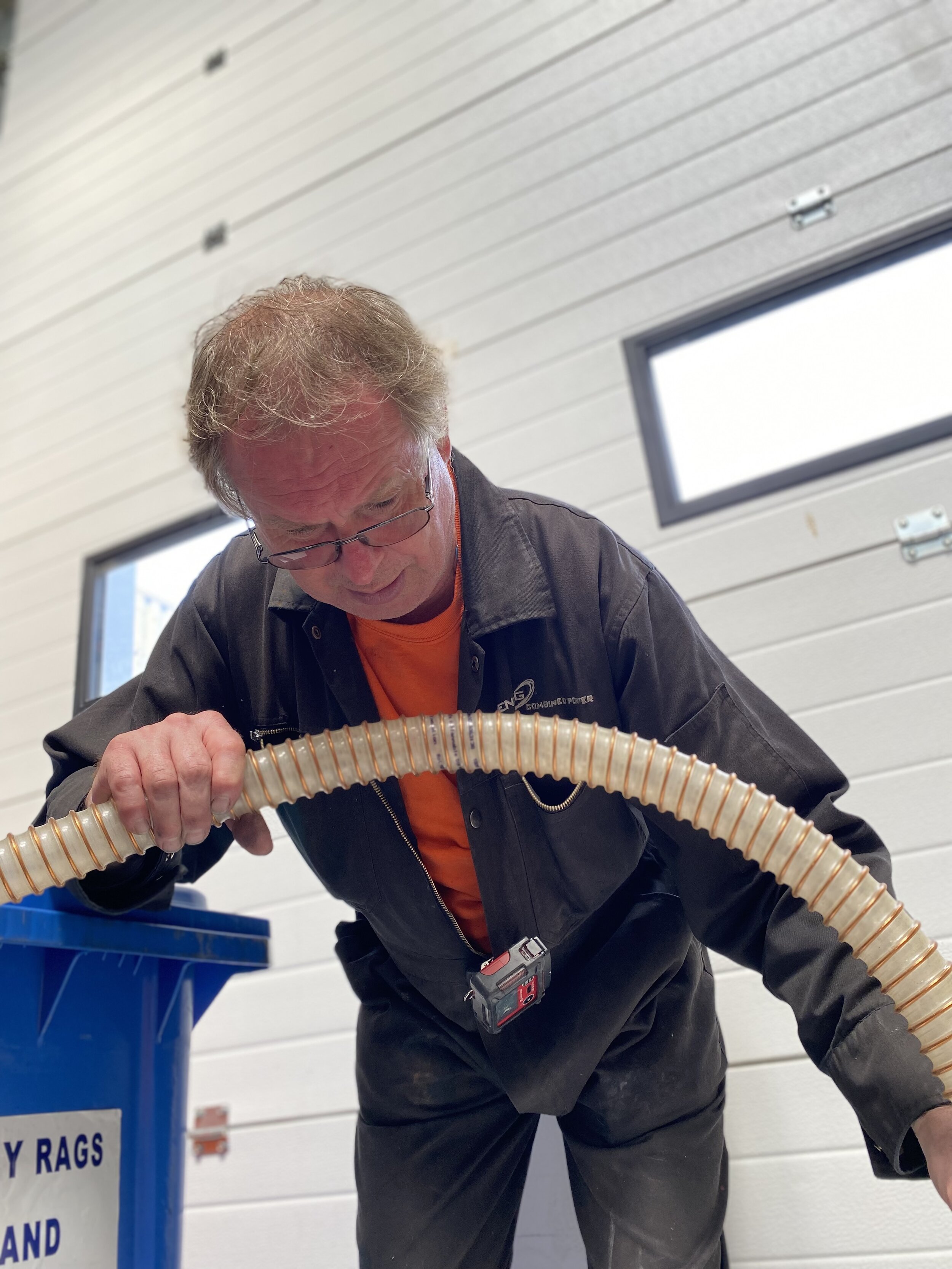
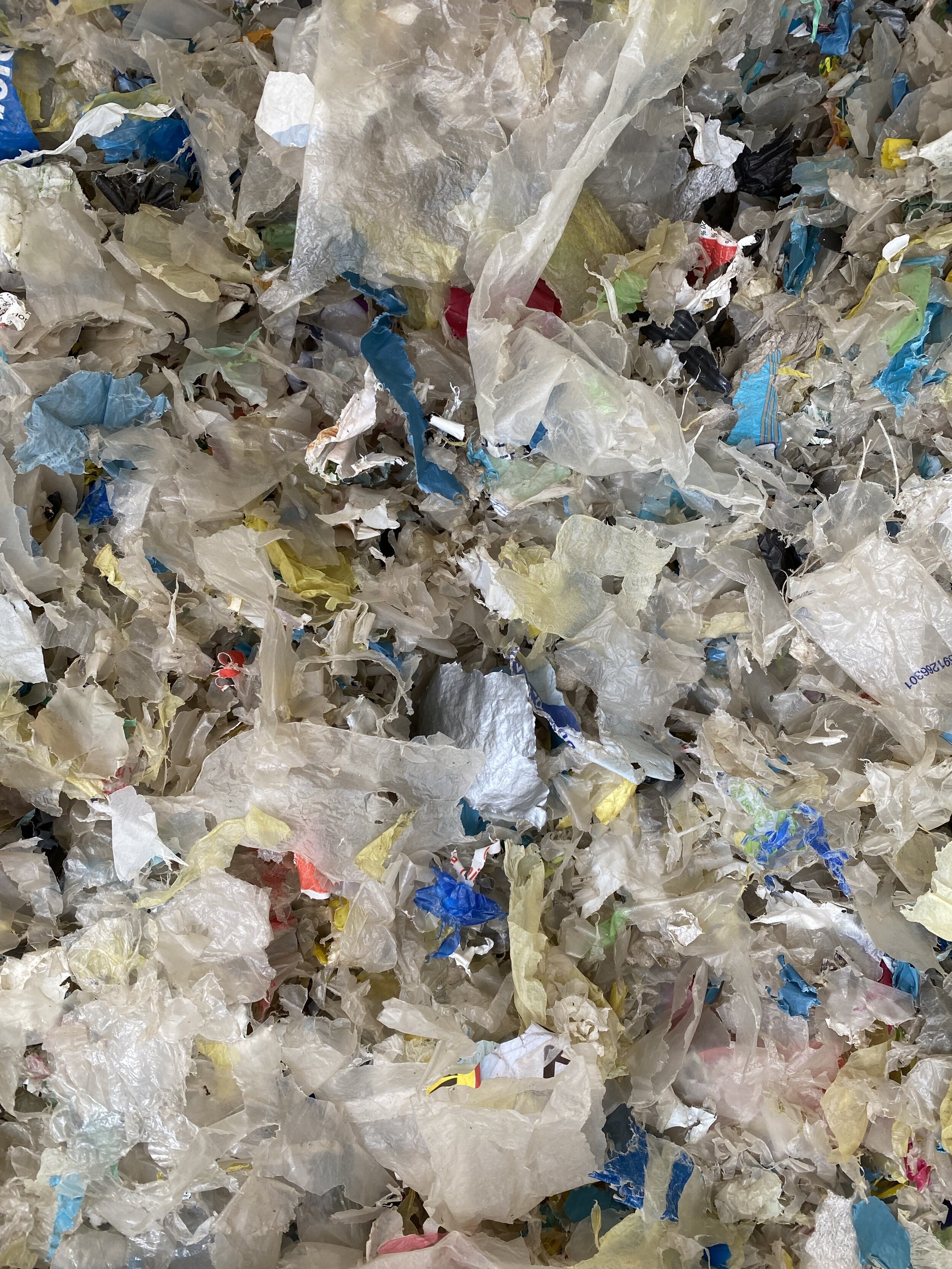
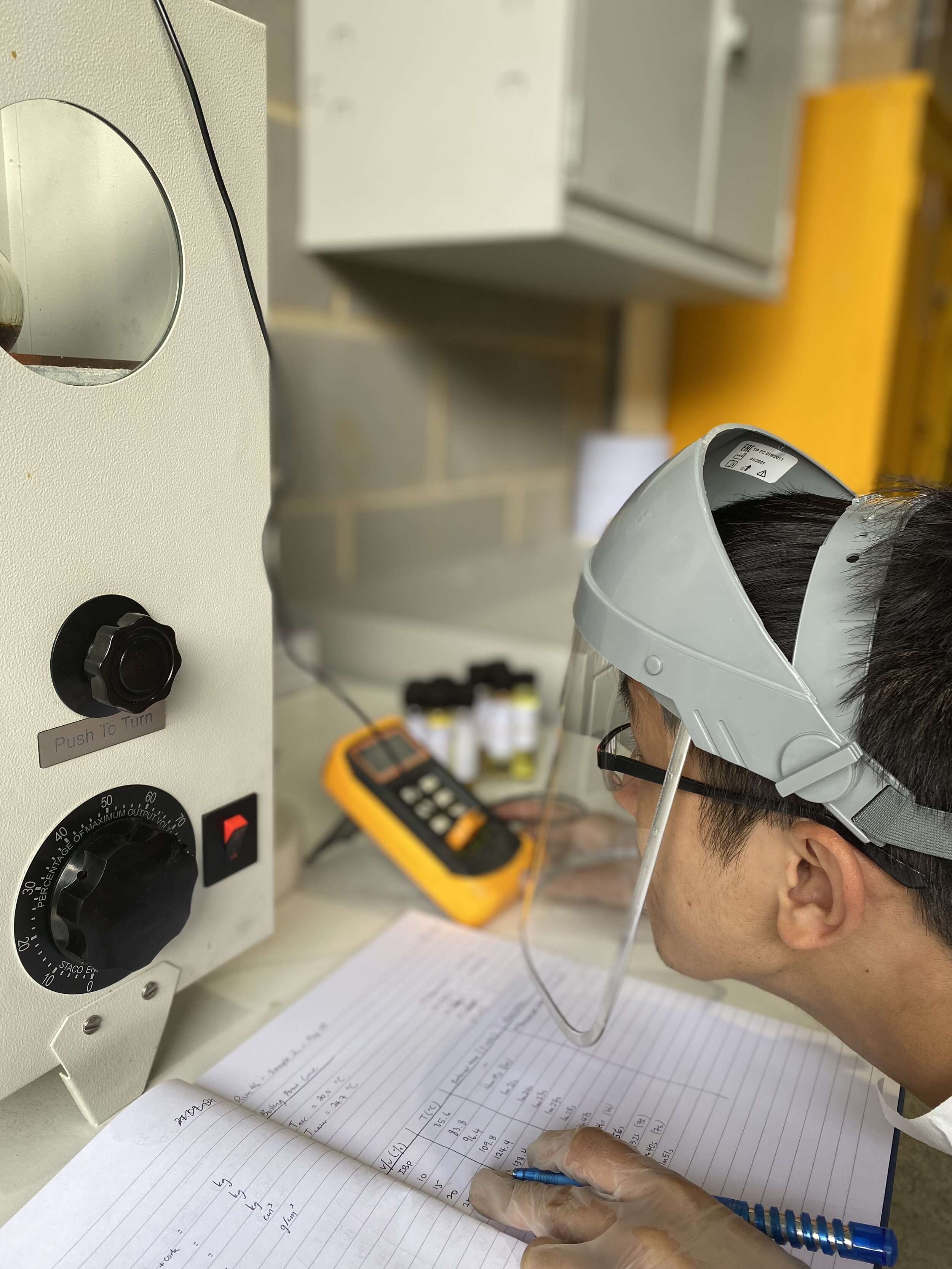
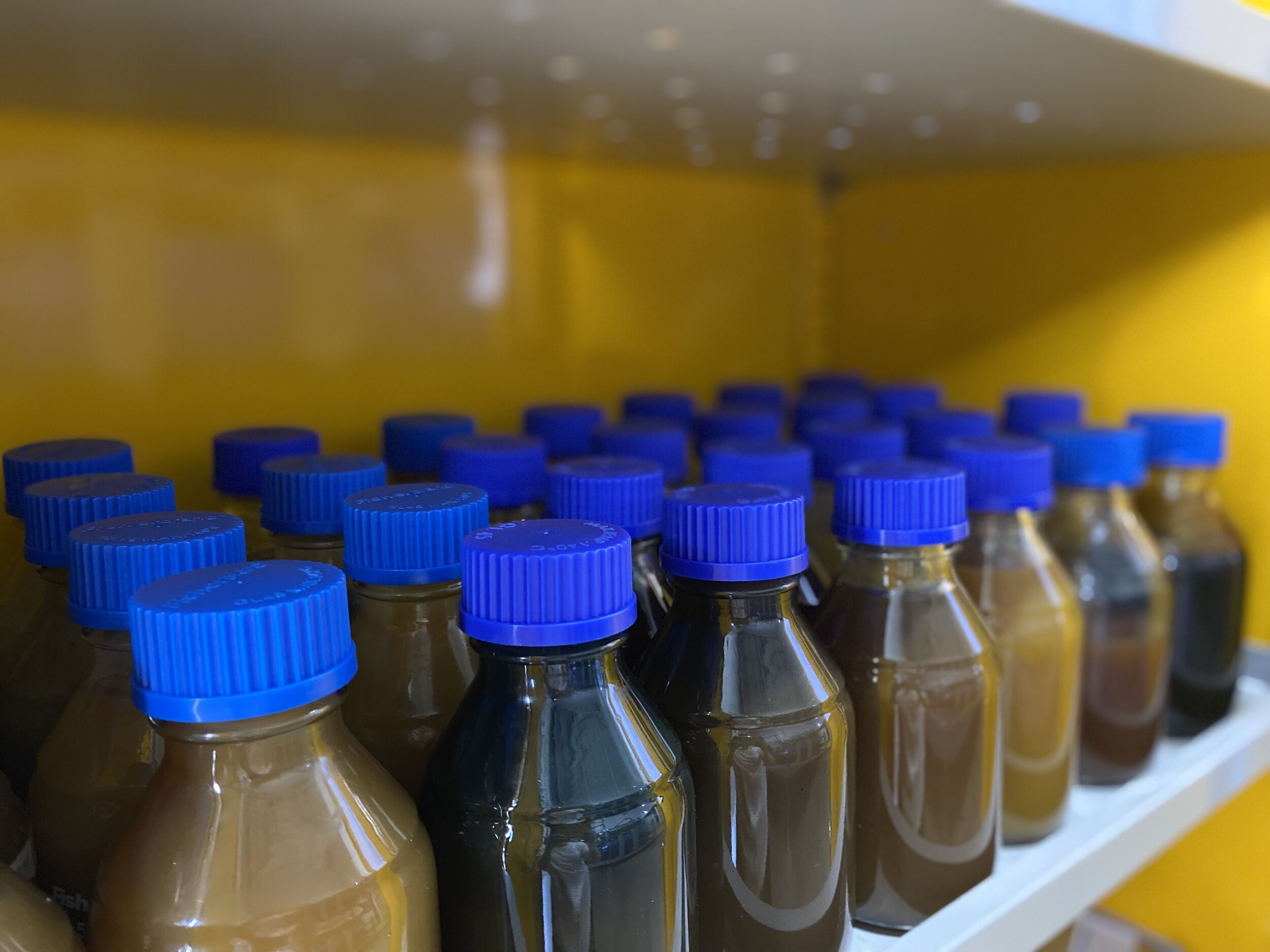
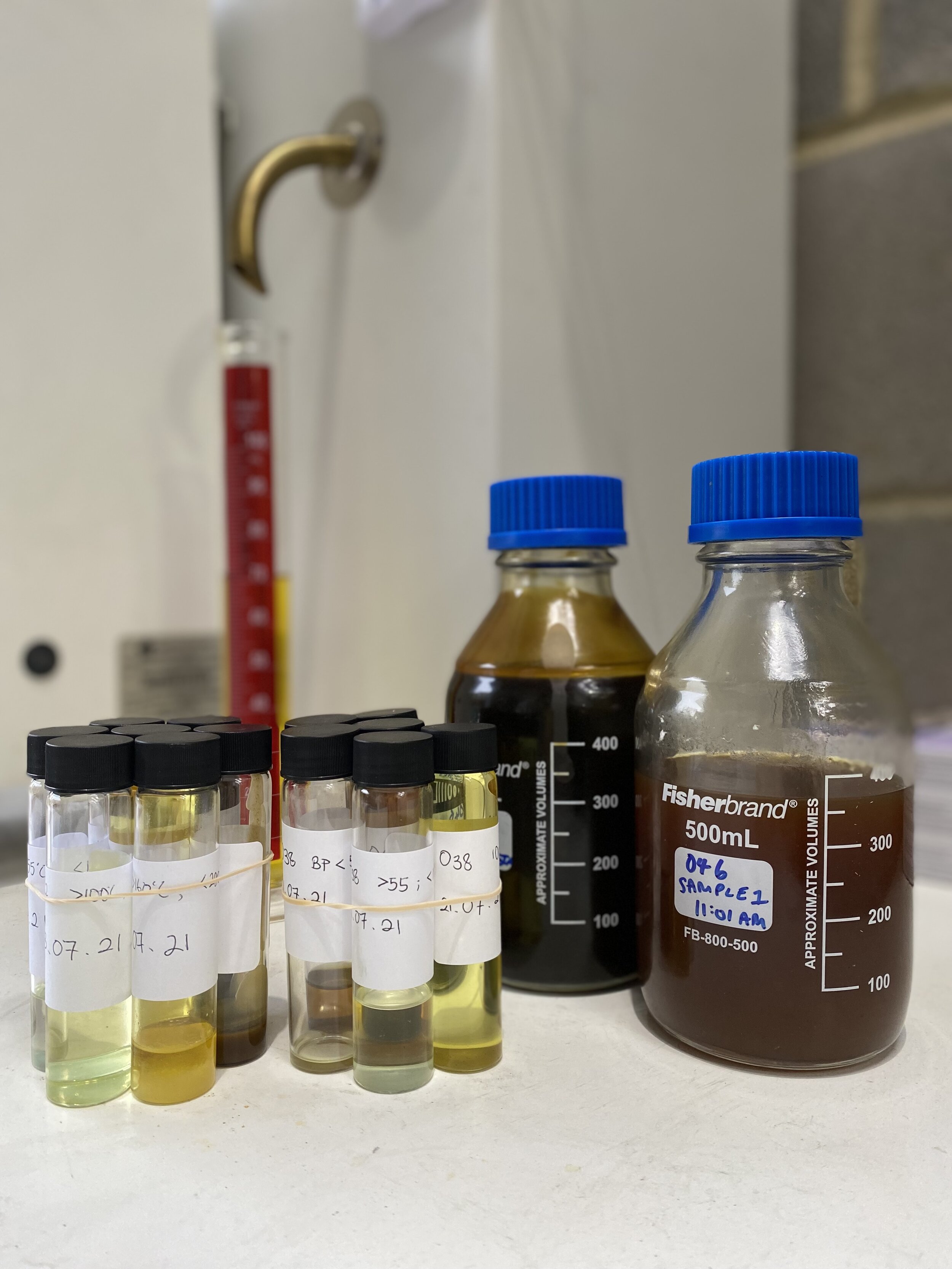
Offtake
On-site distillation gives us preliminary insights into our products, however given the plethora of specifications required for our diverse customers, further laboratory analysis is required. To avoid the significant time and financial implications of further testing, we are partnering with Intertek to produce a real-time oil analysis solution. Built on state-of-the-art topological modelling, we will be able to produce fast and accurate data for measuring particular oil properties. Quality data then enables us to efficiently characterise oil compositions and their marketability. To train the algorithm underpinning the model with enough data to create correlations and therefore predictions, we have carefully controlled the feedstocks, contaminants and operating conditions in generating oil samples of a sufficiently wide spectrum of characteristics.
We are also working closely with petrochemical partners to assess the quality of our products and investigate customer specific properties that are beyond the scope of our “in-house” testing. We operate on a principal of openness and inclusion of our partners in the improvement of our process, and therefore products – in doing this we both leverage different skillsets in the ecosystem and build trusting commercial relationships moving forward.
Plant Process
In our plant process where optimising the pyrolysis conditions for yield and oil quality is key, we face the age-old problem of which dial to turn, and how much to turn it. This type of multi-dimensional optimisation is a labyrinth. There is potential for false turns and dead ends when considering the many variables that can be manipulated - temperature, heating time, throughput and physical feedstock properties, to name a few.
Over the coming months we are installing upgrades to our plant that will address challenges we have seen in the processing of real post-consumer waste, an example of our R&D leading to improvements in both our understanding and technology.
Feedstock
The third focus of the R&D schedule is specifying and sourcing a plastic waste feedstock for the Brightlands plant. There are many different post-consumer options that may be appropriate as feedstock, and even more post-industrial, as companies search for a recycling solution to their post-use products and manufacturing offcuts that are mechanically unrecyclable. Understanding how each potential feedstock’s contaminants may implicate both product quality and process operation is crucial, and in doing these experiments we are building up a library of results, which will help guide the feedstock strategy of our commercial-scale plant.
What’s Next For Itero
While we develop around key areas, all in service of the delivery of our at-scale demonstration plant in the Netherlands, we are upskilling our team, improving our process, and building cooperative relationships across the plastics value chain. As a company, and as an industry, we might not yet have reached our lofty long-term goals, but we are gathering pace, and the shift to circularity has well and truly started.